As the demand for sustainable food packaging rises, paper lunch box making machines play a central role in eco-conscious production. With a range of forming technologies, servo innovations, and sealing options, understanding how these machines work—and what sets them apart—is essential for food packaging manufacturers. This comprehensive guide explores machine types, servo-driven advantages, sealing methods, and customization capabilities.
Overview of Paper Lunch Box Making Machines
Paper lunch box making machines are essential in the sustainable food packaging industry, enabling efficient production of disposable food containers. These machines differ in their forming mechanisms, speed, materials compatibility, and sealing technologies. Understanding their categories helps manufacturers choose the best fit for their production needs.
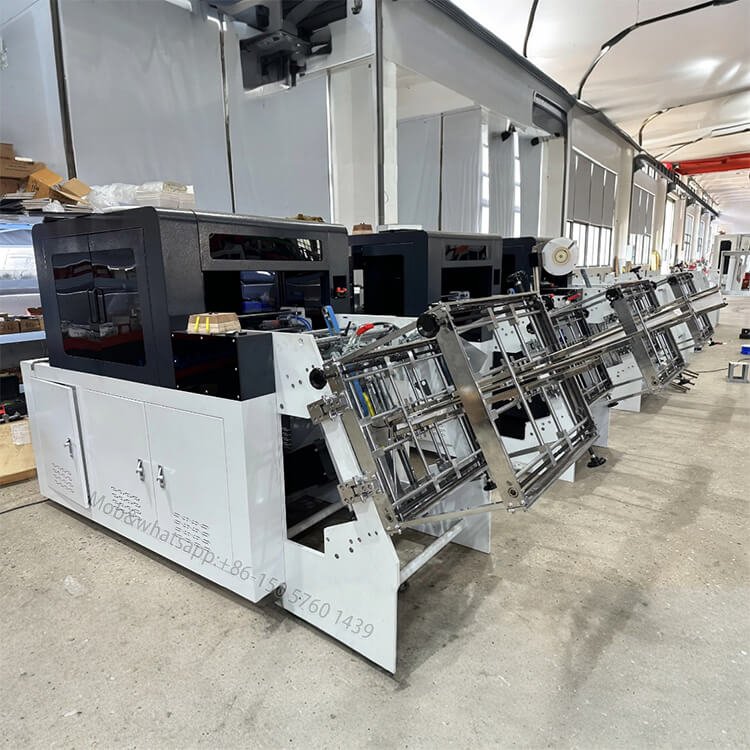
Main Categories of Paper Lunch Box Forming Machines
1. Servo-Driven Forming Machines
- Model: VLB-800
- Speed Range: 50–400 pcs/min
- Compatible Material: Single or double PE-coated paper
- Sealing Method: Water-based glue or hot melt glue
- Key Features:
- Precise servo control for all forming steps
- Smart PLC and HMI interface for easy operation
- Versatile shape production with fast format changes
- Low maintenance and quieter operation
2. Double Lane Machines
- Model: VLB-1400
- Speed Range: Up to 800 pcs/min
- Compatible Material: Single or double PE-coated paper
- Sealing Method: Water-based glue or hot melt glue
- Key Features:
- Two independent servo-controlled forming lanes
- High efficiency and throughput for large-scale production
- Reduced maintenance and energy consumption
- Ideal for multi-shape, multi-design orders
3. Mechanical food tray making machine
- Model: VFT
- Speed Range: 30–45 pcs/min
- Compatible Material: PE-coated paper
- Sealing Method: Hot air sealing
- Key Features:
- Mechanical drive, no compressed air needed
- Lower operational costs and energy use
- Simple and cost-effective design
- Suitable for standard food trays, hamburger boxes, and takeaway containers
4. Thermoforming Units
- Model: VLB-500
- Speed Range: 30–60 pcs/min
- Compatible Material: PE-coated paper (200–400g/m²)
- Sealing Method: Hot air or hot press sealing
- Key Features:
- Air-assisted forming with stable heating
- Consistent forming quality for single-compartment boxes
- Requires compressed air supply
- Ideal for water-resistant disposable containers
Summary Table of Machine Types
Machine Type | Speed Range | Compatible Material | Sealing Method | Key Features |
---|---|---|---|---|
Servo-Driven Forming Machines | 50–400 pcs/min | Single/double PE-coated paper | Water glue/hot melt glue | Servo precision, smart control, shape versatility |
Double lane Machines | Up to 800 pcs/min | Single/double PE-coated paper | Water glue/hot melt glue | High-efficiency, low maintenance |
Mechanical Systems | 30–45 pcs/min | PE-coated paper | Hot air | No air needed, lower cost |
Thermoforming Units | 30–60 pcs/min | PE-coated paper (200–400g/m²) | Hot air/hot press | Air-assisted, stable heating & forming |
Conclusion
Paper lunch box forming machines are available in a variety of designs tailored to production scale, box complexity, and material type. Whether you’re producing basic trays or customized, multi-compartment containers, the right technology—be it servo-driven or mechanically operated—can enhance output quality, reduce waste, and improve operational efficiency. Selection ultimately depends on your production goals, packaging requirements, and material preferences.
Types of VLB Lunch Box Making Machines
To meet diverse packaging needs, VLB lunch box forming machines are classified into multiple categories based on sealing technology, drive system, and production scale. Below is an overview to help choose the right solution.
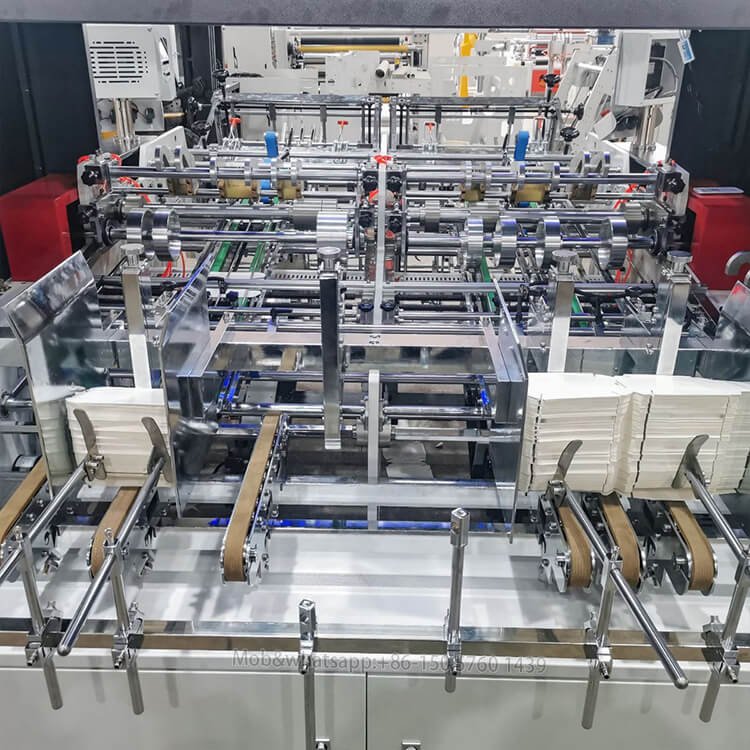
1. VLB-800: Servo Lunch Box Forming Machine
Sealing Method: Water-based glue (Hot melt glue optional)
Material: Carton board (200–600 gsm)
Drive System: Fully servo-driven
Speed: 60–160 pcs/min
Max Forming Size: 450×580 mm
Advantages:
- Four independent servo motors for high precision
- PLC+HMI intelligent control
- Easy mold change for different box types
- Lower maintenance and noise
- Suitable for burger boxes, trays, food pails
2. VLB-1400: Dual-Lane Servo High-Speed Machine
Sealing Method: Water-based glue (Hot melt glue optional)
Material: Carton board (200–600 gsm)
Drive System: Dual servo lines with independent control
Speed: Up to 300 pcs/min (150 pcs/min per line)
Key Features:
- Two independent forming stations for higher output
- Multi-shape production at the same time
- Servo-actuated precision forming, gluing, folding, and stacking
- Remote monitoring and real-time diagnostics
- Ideal for high-volume, multi-size lunch box manufacturing
3. VLB-500: Mechanical Hot Sealing Machine
Sealing Method: Hot Sealing
Material: PE-coated paper (200–400 g/m²)
Drive System: Mechanical
Speed: 30–45 pcs/min
Forming Area: Up to 500×500 mm
Features:
- Ideal for small to medium-volume production
- Simple operation, no air compressor required
- Energy-saving and durable
- Suitable for standard hamburger and takeout boxes
Summary Comparison Table
Model | Speed | Sealing Method | Material | Drive System | Application Scope |
---|---|---|---|---|---|
VLB-500 | 30–45 pcs/min | Hot sealing | PE-coated paper (200–400 g/m²) | Mechanical | Entry-level, low-cost production |
VLB-800 | 60–160 pcs/min | Water-based glue / hot melt | Carton board (200–600 gsm) | Fully servo-driven | Medium to high-speed, flexible production |
VLB-1400 | Up to 300 pcs/min | Water-based glue / hot melt | Carton board (200–600 gsm) | Dual servo lines | High-speed, multi-shape mass production |
What are the common sealing methods used in lunch box forming machines?
Sealing plays a critical role in the performance and durability of paper lunch boxes. Different machines use different sealing technologies based on their design, material compatibility, and production goals.
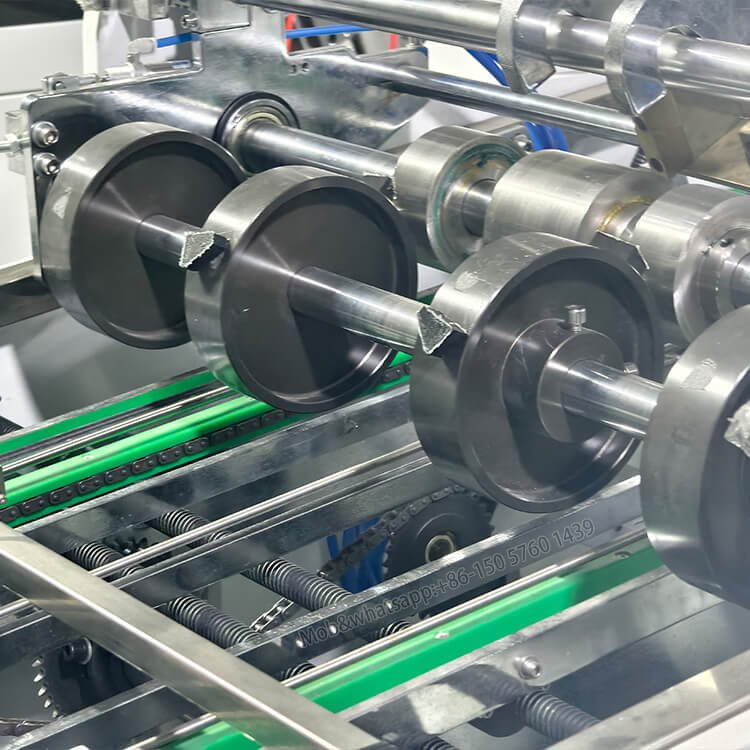
Hot sealing is a traditional method using thermal compression to bond PE-coated paper. It’s straightforward, reliable, and ideal for basic take-out containers.
Water-based glue is commonly used in servo-driven machines, offering environmentally friendly sealing with flexible mold shaping—ideal for thicker carton boards and complex shapes.
Hot melt glue, available as an option in advanced models, offers strong adhesion and fast drying, especially suitable for specialty papers and PE-coated substrates.
Each method has its unique strengths and is chosen based on the target product type, speed, and sustainability goals.
Sealing Method | Compatible Models | Materials | Strengths / Advantages | Typical Application |
---|---|---|---|---|
Hot Sealing | VLB-500, Thermoforming Units | PE-coated paper | Simple, reliable thermal bonding | Reliable sealing with thermal compression |
Water-Based Glue | VLB-800, VLB-1400 | Carton board (200–600 gsm) | Eco-friendly, mold flexibility, low thermal impact | Used in servo-driven machines |
Hot Melt Glue (Option) | VLB-800, VLB-1400 | PE/specialty paper | Fast drying, strong adhesion | Optional on servo models |
How Servo-Driven Technology Improves Lunch Box Machines
1. Independent Control of Each Component
Each step—feeding, cutting, forming, sealing—is servo-controlled independently:
- Precise paper feed alignment
- Accurate blanking die operation
- Optimized forming pressure and stroke
- Efficient discharge and stacking
This modular control improves precision and synchronization.
2. Higher Quality, Lower Defect Rate
Servo-driven motion ensures:
- Smoother forming cycles
- Uniform box shapes and tight sealing
- Reduced material waste and fewer rejects
3. Faster Production with Flexible Timing
- Dynamic stroke/dwell time adjustments
- Faster tooling changeovers
- Reduced vibration, enabling higher throughput
4. Quieter and Low-Maintenance Operation
- Minimal vibration and mechanical friction
- Lower noise levels and wear
- Extended equipment lifespan
5. Smart Control & Monitoring
- Integrated PLC + HMI touchscreen
- Real-time production data
- Fault detection and remote access support
6. Quick Adaptation for Custom Shapes
- Easy profile change via software
- No need for cam reconfiguration
- Faster response to market or seasonal design changes
Why Choose Servo-Driven VLB Machines?
Servo-driven systems represent a significant technological advancement over traditional mechanical lunch box forming machines. Their design and operation provide several important benefits that enhance productivity, quality, and ease of use in modern packaging production.
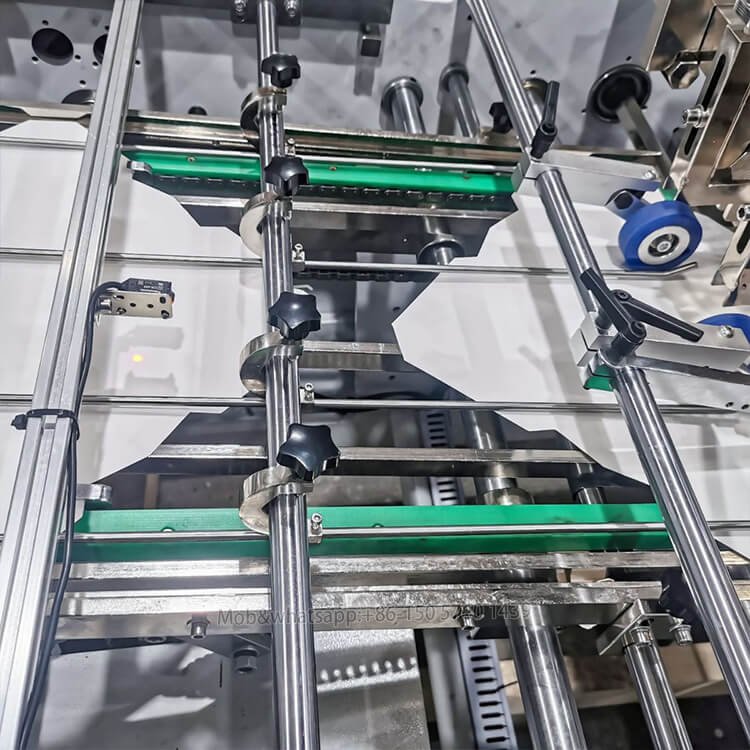
1. Independent Module Control for Greater Precision
Each key process—feeding, gluing, folding, ejecting—is controlled by dedicated servo motors. This modular control allows precise timing and synchronization, minimizing errors and ensuring consistent product quality. It also enables customization of each step to meet specific product requirements, such as multi-compartment boxes or complex shapes.
2. Faster Mold Changeovers and Enhanced Flexibility
Servo technology allows quick and easy adjustments to machine settings through software, reducing downtime significantly. Mold changes and size adaptations can be performed rapidly without extensive mechanical modifications, making the machines highly versatile for small batch runs or seasonal design variations. This flexibility supports manufacturers in responding promptly to market demands.
3. Higher Accuracy with Reduced Material Waste
Servo-driven machines offer superior repeatability and consistent force application during forming and sealing. This accuracy ensures tight seals and precise cuts, reducing rejects and minimizing material wastage. The result is not only cost savings but also better environmental sustainability through efficient resource use.
4. Smart Interface for Real-Time Monitoring and Diagnostics
Equipped with advanced PLC and HMI touchscreen controls, these machines provide real-time production data and diagnostics. Operators can monitor parameters such as speed, temperature, and error codes instantly, enabling quicker troubleshooting and reducing downtime. Some systems also support remote access for maintenance and software updates.
5. Lower Noise, Longer Lifespan, and Reduced Mechanical Wear
Servo motors operate smoothly with less vibration compared to traditional mechanical cams and linkages. This reduces noise levels on the production floor and decreases wear on components, leading to extended equipment life and less frequent maintenance. The quieter, more reliable operation enhances the working environment and lowers overall operating costs.
6. Energy Efficiency and Reduced Air Consumption
Many servo-driven machines require less compressed air or none at all, lowering energy consumption. This contributes to a greener production process and reduces operational expenses.
Summary:
Choosing servo-driven VLB lunch box machines means investing in precision, efficiency, and flexibility. These systems empower manufacturers to meet demanding production schedules, maintain high product quality, and adapt quickly to changing market needs—all while reducing waste and operational costs.
Application Examples of Paper Lunch Box Making Machines
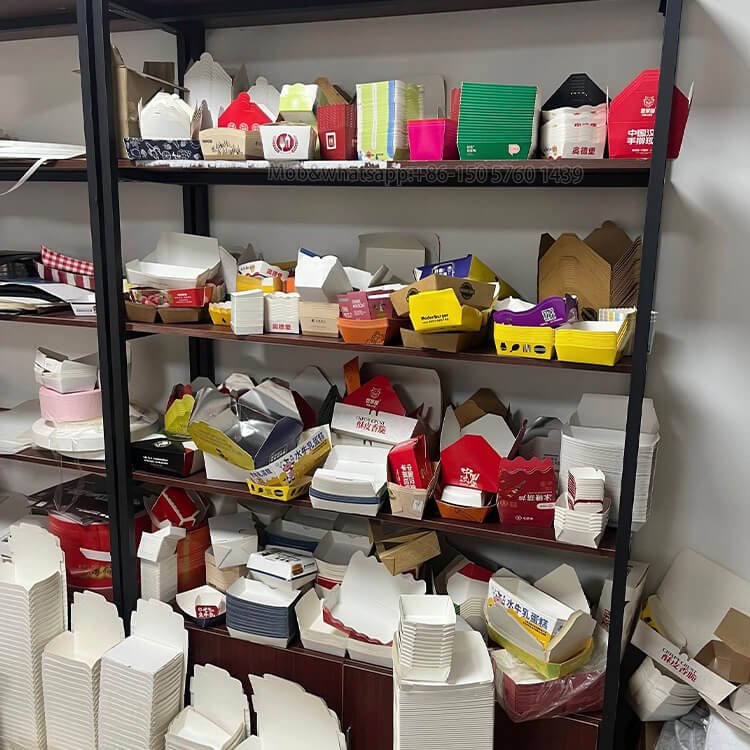
1. Takeout Food Trays
Takeout trays are widely used in fast-food restaurants, cafeterias, and catering services to provide convenient, disposable packaging for a variety of dishes. These trays are typically designed with durability and spill-resistance in mind, often using PE-coated paper to ensure water and grease resistance. Machines producing these trays must deliver consistent forming and sealing to maintain product integrity during transport and consumption.
2. Burger and Sandwich Boxes
Burger and sandwich boxes require precise forming to securely hold the food items without crushing or losing heat. These boxes often have specialized shapes, such as hinged lids or locking tabs, to improve user convenience. Servo-driven machines excel in producing these complex shapes quickly and with high accuracy, ensuring tight seals and attractive presentation for fast-food chains and takeout services.
3. Multi-Compartment Lunch Boxes
Multi-compartment boxes are essential for meal variety, allowing different foods to be separated without mixing flavors or moisture. Commonly used in meal delivery, school lunches, and corporate catering, these containers must have strong seals between compartments and sturdy construction. Advanced machines capable of handling customizable molds and high-frequency sealing are ideal for producing these versatile boxes at various production scales.
4. Paper Pails and Snack Containers
Paper pails and snack containers are popular for packaging items like popcorn, chips, nuts, and other dry snacks. These containers require precise forming to maintain shape and prevent leakage. The sealing methods used, such as water-based or hot melt glues, ensure secure adhesion while supporting easy opening for consumers. Machines capable of handling thicker carton board materials and varied container sizes are preferred for this application.
These application examples showcase the versatility of paper lunch box making machines in meeting diverse packaging needs across the food industry. Whether producing simple trays or intricate multi-compartment containers, these machines deliver reliable performance and eco-friendly solutions that align with modern consumer demands.
Why Independent Actuator Control Matters for Customization in Lunch Box Forming Machines
In today’s fast-paced food packaging industry, the demand for personalized, multi-format containers is on the rise. Whether it’s a custom-branded burger box, a snack tray with compartments, or a specialty take-out container, manufacturers need lunch box forming machines that offer flexibility without sacrificing speed or accuracy. This is where independent actuator control—powered by servo motors—makes a significant difference.
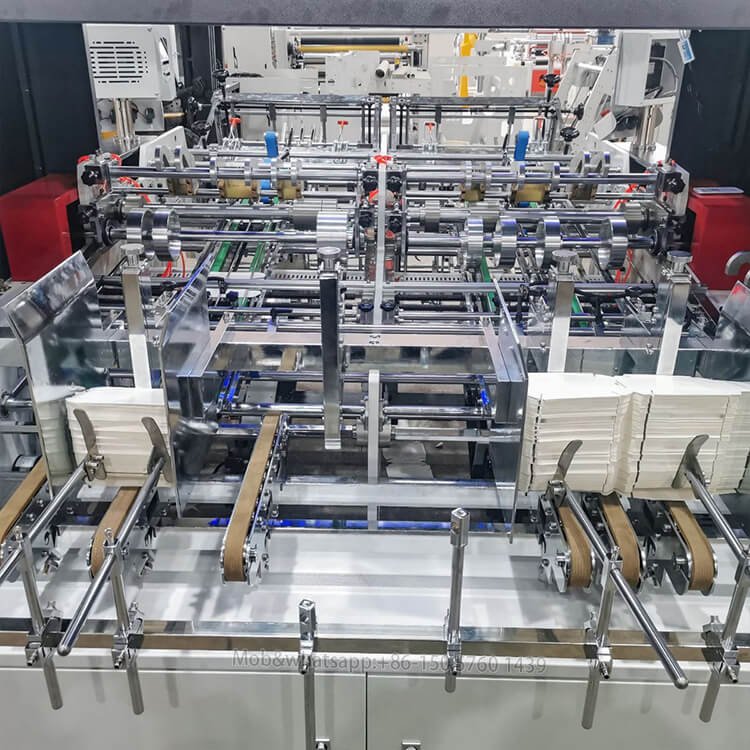
What Is Independent Actuator Control?
Unlike traditional mechanical systems where all movements are linked and driven by a single motor or cam, servo-driven forming machines feature individual servo actuators for each motion module. That means feeding, pressing, gluing, folding, and ejecting are all controlled independently, and precisely.
Key Advantages of Independent Actuator Control
- Programmable Precision for Each Production Step
Each actuator operates independently and can be finely programmed, ensuring consistent quality and minimizing material waste. This is especially beneficial when producing customized lunch boxes of varying sizes and complex shapes. - Smooth Synchronization for Complex Designs
Independent control makes it easier to synchronize operations required for multi-compartment or irregularly shaped boxes, enhancing versatility without sacrificing speed or quality. - Fast and Flexible Format Changes
Quick mold swaps and adjustable machine settings reduce downtime, supporting both small batch runs and large-scale production with ease. - Advanced Automation and Smart Feedback
Integrated sensors and intelligent control systems provide real-time monitoring and diagnostics, improving uptime and reducing the need for manual intervention.
Why It Matters
For food packaging manufacturers who prioritize customization, speed, and quality, independent actuator control is a game-changer. It empowers businesses to:
- Expand their product line with new container styles
- Serve custom orders with short lead times
- Maintain high precision even at high speeds
- Reduce operational costs associated with setup and maintenance
This level of modular flexibility and automation intelligence is especially valuable in today’s market, where packaging design is a key part of the brand experience.
Impact on Production
With independent servo actuator control like that in the VLB-1400, manufacturers can achieve higher productivity and superior product quality. This technology supports efficient, high-precision manufacturing of customized box shapes that traditional mechanical linkages struggle to handle, making it an essential feature for modern lunch box forming equipment.
VLB-1400: A Leading Example of Independent Actuator Control Technology
VIE Machinery’s VLB-1400 lunch box forming machine features this advanced independent actuator control system. This model delivers exceptional flexibility and precision, enabling manufacturers to efficiently produce a wide variety of customized box shapes—including multi-compartment and complex designs—at high speeds. Its dual-lane configuration further boosts productivity while maintaining excellent quality and low waste.
Summary Table: Servo Actuator Control vs. Mechanical Linkages
Feature | Independent Actuator (Servo) | Traditional Mechanical Linkage |
---|---|---|
Movement Control | Individually programmable | Shared drive, limited flexibility |
Format Changeover | Quick, digital adjustment | Manual, time-consuming setup |
Custom Box Compatibility | High (including multi-compartment) | Low to moderate |
Precision and Repeatability | Excellent | Moderate |
Maintenance Requirements | Lower (less mechanical wear) | Higher (more moving parts) |
Automation & Feedback | Real-time monitoring and diagnostics | Limited or none |
By investing in servo-driven lunch box forming machines like the VLB-1400, manufacturers gain the flexibility and precision needed to stay competitive in a fast-evolving market where custom food packaging solutions are increasingly in demand.
Finding the Right Machine for Your Needs
For paper food container manufacturers, choosing the correct forming machine impacts speed, customization, and quality. Here’s a quick decision guide:
- Startups & Medium Output: VLB-500 offers solid mechanical performance with heat sealing.
- High-Speed Precision: VLB-800 is ideal for rapid production and glue sealing.
- Large-Scale & Multi-Shape Runs: VLB-1400 delivers dual-lane flexibility, servo precision, independent actuator control and versatility, and the highest productivity.
Production Scale | Best Model | Key Advantage |
---|---|---|
Small to Medium | VLB-500 | Low-cost, compact, simple mechanical operation |
Medium to Large | VLB-800 | Servo control with water/hot melt glue option |
Mass & Multi-format | VLB-1400 | Dual-lane high-speed production with independent actuator control and versatility |
Explore VIE Machinery to find a complete range of paper lunch box forming solutions.